Professional Guidance on What is Porosity in Welding and Just How to Address It
Wiki Article
The Science Behind Porosity: A Comprehensive Guide for Welders and Fabricators
Understanding the elaborate mechanisms behind porosity in welding is critical for welders and producers striving for remarkable craftsmanship. From the make-up of the base products to the intricacies of the welding procedure itself, a multitude of variables conspire to either aggravate or alleviate the visibility of porosity.Recognizing Porosity in Welding
FIRST SENTENCE:
Evaluation of porosity in welding exposes critical insights into the integrity and high quality of the weld joint. Porosity, identified by the visibility of tooth cavities or voids within the weld steel, is an usual worry in welding procedures. These voids, otherwise appropriately attended to, can compromise the architectural stability and mechanical residential or commercial properties of the weld, causing prospective failings in the completed product.
To discover and quantify porosity, non-destructive testing methods such as ultrasonic testing or X-ray inspection are frequently utilized. These techniques enable for the identification of internal defects without endangering the stability of the weld. By examining the dimension, shape, and distribution of porosity within a weld, welders can make informed decisions to enhance their welding processes and accomplish sounder weld joints.
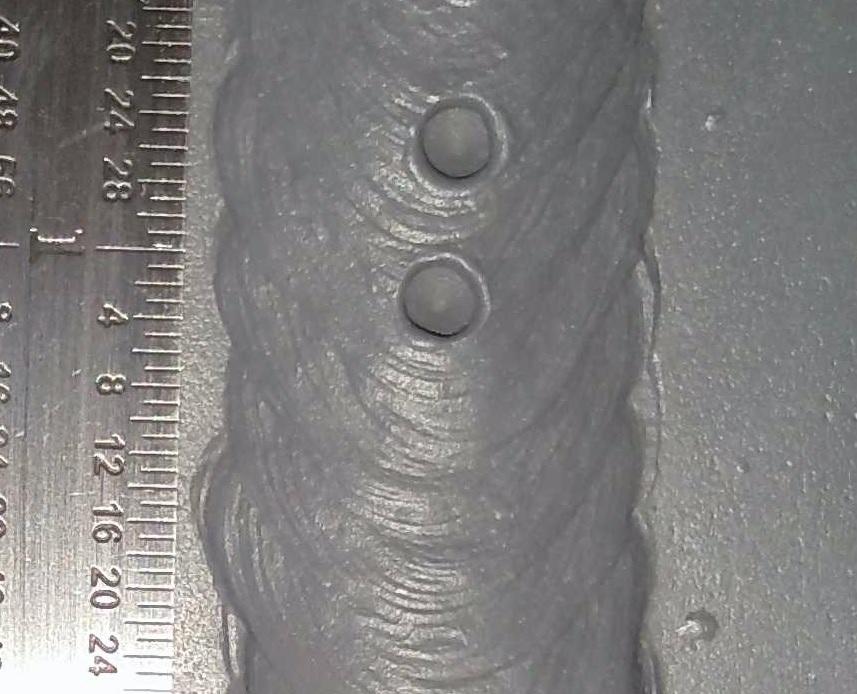
Aspects Influencing Porosity Formation
The event of porosity in welding is affected by a myriad of aspects, ranging from gas shielding effectiveness to the intricacies of welding specification settings. One essential element contributing to porosity formation is insufficient gas shielding. When the protecting gas, commonly argon or carbon dioxide, is not effectively covering the weld swimming pool, atmospheric gases like oxygen and nitrogen can infect the liquified metal, resulting in porosity. In addition, the cleanliness of the base products plays a significant duty. Impurities such as rust, oil, or dampness can vaporize throughout welding, developing gas pockets within the weld. Welding specifications, consisting of voltage, existing, travel speed, and electrode type, also impact porosity formation. Utilizing inappropriate settings can produce extreme spatter or warmth input, which subsequently can cause porosity. Furthermore, the welding strategy employed, such as gas metal arc welding (GMAW) or shielded steel arc welding (SMAW), can affect porosity development as a result of variants in warmth circulation and gas protection. Understanding and regulating these elements are essential for minimizing porosity in welding procedures.Impacts of Porosity on Weld High Quality
The visibility of porosity likewise deteriorates the weld's resistance to rust, as the caught air or gases within the voids can respond with the surrounding atmosphere, leading to degradation over time. Additionally, porosity can prevent the weld's capability to withstand stress or effect, further threatening the general quality and integrity of the welded structure. In essential applications such as aerospace, vehicle, or structural building and constructions, where security and resilience are extremely important, the damaging effects of porosity on weld top quality can have serious effects, highlighting the significance of decreasing porosity with correct welding strategies and procedures.Strategies to Reduce Porosity
Furthermore, utilizing the appropriate welding specifications, such as the right voltage, existing, and travel speed, is essential in stopping porosity. Keeping a regular arc length and angle during welding also helps decrease the probability blog here of porosity.
Using the appropriate welding strategy, such as back-stepping or utilizing click here to read a weaving motion, can also aid disperse warm evenly and minimize the chances of porosity development. By executing these methods, welders can efficiently minimize porosity and generate premium welded joints.
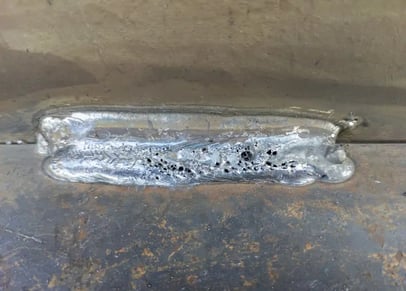
Advanced Solutions for Porosity Control
Carrying out advanced technologies and innovative techniques plays a critical duty in achieving remarkable control over porosity in welding processes. One sophisticated solution is the usage of sophisticated gas mixes. Shielding gases like helium or a combination of argon and hydrogen can assist decrease porosity by providing far better arc stability and improved gas insurance coverage. Furthermore, employing innovative welding methods such as pulsed MIG welding or modified ambience welding can likewise aid minimize porosity issues.Another sophisticated remedy entails the use of innovative welding devices. For example, utilizing tools with built-in functions like waveform control and innovative source of power can boost weld quality and minimize porosity threats. In addition, the application of automated welding systems with specific control over parameters can significantly reduce porosity problems.
In addition, including innovative surveillance and assessment modern technologies such as real-time X-ray imaging or automated ultrasonic screening can help in identifying porosity early in the welding process, permitting immediate restorative activities. On the whole, integrating these sophisticated remedies can significantly boost porosity control and enhance the overall quality of bonded parts.
Conclusion
In conclusion, recognizing the scientific research behind porosity in welding is vital for welders and fabricators to generate premium welds - What is Porosity. Advanced solutions for porosity control can additionally Bonuses enhance the welding procedure and make certain a solid and reputable weld.Report this wiki page